IATF16949 취득업체라면 고객으로부터 PPAP심사를 받게 됩니다. PPAP을 받을 경우 어떤 사항을 준비해야 할지 막막하실 텐데 아래 정보를 기반으로 준비하시면 도움이 되실 겁니다.
PPAP이란?
PPAP은 Production Part Approval Process(생산부품 승인 절차)로 IATF16949에서 요구하는 필수 항목입니다. GM, Ford 등 북미의 자동차 업체가 요구하는 신규 부품의 승인 절차입니다. 현대기아차 그룹(HKMC)에서는 ISIR(Initial Sample Inspection Report)이라고 표현하지만 모두 동일한 역할을 한다고 보시면 됩니다. 모두 협력업체가 고객이 원하는 제품을 생산할 수 있는 공정을 가지고 있는지(공정 타당성), 원하는 제품 사양을 안정적으로 생산할 수 있는지(제품 타당성)를 확인하기 위해 본 절차를 마련한 것입니다.
PPAP의 절차
PPAP은 APQP(사전 부품 승인 절차)에서 가장 마지막 단계에 위치한 고객의 승인 절차입니다. 그렇기 때문에 APQP부터 간단히 이해를 하고 넘어가셔야 합니다. APQP는 사전 부품 승인절차입니다. 우리가 고객이 요구하는 신규 제품을 개발할 시에 이 절차를 통해 제품을 생산하는 데 문제가 없는지 양산하기 전에 검증을 하는 과정입니다. 양산 시작(SOP; Start Of Production) 후 문제가 발생하면 그 이상의 대가를 치를 수 있기 때문입니다.
PPAP심사 시에는 양산에 준하는 생산을 진행해야 합니다. 최소 1시간에서 8시간까지의 300ea를 생산하게 됩니다. 하지만 위 생산 기준은 제품군에 따라 다르게 적용되니 고객 요구사항을 따라 진행하면 됩니다. 1개 Lot를 생산하는 데에 8시간 이상 소요되는 경우 일부 Lot를 생산하여 샘플링 수를 늘려서 진행하는 경우도 있습니다. 최소 30개 이상의 data를 추출하여 초기 공정능력을 평가하게 됩니다. PPAP심사가 끝난 뒤 공정능력을 평가하여 고객이 요구하는 공정능력을 만족해야 합니다. 공정능력에 대한 요구사항도 고객별로 상이하기 때문에 고객이 요구하는 수준 이상으로 나와야 합니다. 물론 내부 기준을 만족시켜야 합니다. 일반적으로 Cpk 1.67 이상을 기준으로 잡긴 합니다. 기준이 높다고 생각하실 수 있지만 양산을 진행하게 되면 일반적으로 다양한 외부요인으로 인해 산포가 증가하기 때문입니다.
PPAP 제출 문서(산출물)
PPAP을 진행할 경우 아래의 요구하는 문서를 제출해야 합니다. 하지만 항상 모든 항목을 제출하는 것은 아니고 설계 수준에 따라 제출하는 문서가 상이합니다. 완전히 새로운 제품을 개발하는 경우 수준이 높아져 모든 문서를 거의 제출해야 하지만 일분 설계변경만 일어나는 경우 간소화된 문서만 제출하면 됩니다. 각 수준별로 기준을 정하여 제출할 문서가 정해져 있으니 PPAP 진행 시 어느 수준에 해당하는지 고객과 협의하시고 자료를 준비하시면 됩니다. 아래의 자료를 준비하셔야 하니 참고 부탁드리며 문의사항이 있으실 경우 댓글로 남겨주세요.
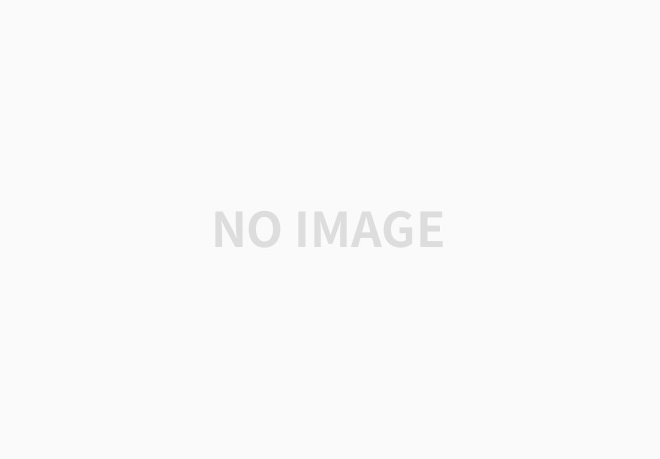
1. Design record(설계 기록)
제품 구성품에 대한 설계 기록을 의미합니다. 도면 및 수치가 나와있는 계산서라고 보면 됩니다. Bulk자재 또는 화학제품일 경우 화학식 및 공정의 단계 등을 포함해야 합니다.
2. Engineering Change Approval(엔지니어링 변경 승인)
고객이 요구한 품질, 안정성 및 규제, 내구성(신뢰성)을 만족하는지 고객 R&D부서의 승인을 득한 결과를 말합니다.
3. Engineering Change Document(엔지니어링 변경 문서)
설계 기록에 반영되지 않지만 실제 구성 부품에 반영된 엔지니어링 변경 문서를 말합니다. 해당되는 경우에 제출하시면 됩니다.
4. Design FMEA(설계 FMEA)
설계 시 제품 디자인의 Risk를 검토했는지를 판단하는 자료입니다. IATF16949에 해당하는 경우 RPN을 산출하여 Risk를 평가하고 개선한 이력이 확인되어야 합니다. VDA6.3에 해당하는 경우 AP(Action Priority)를 정하여 우선순위가 높은 사항에 대해서 개선을 진행해야 합니다. 이러한 이력이 사전에 확인되어야 Risk 평가가 적절히 되었다고 판단할 수 있습니다. Risk 평가만 진행하고 실행한 이력이 없다면 이 또한 문제가 될 수 있으니 개발 당시에 Risk 검토를 진행하고 개선 검토 및 실행한 이력을 기록해야 합니다.
5. Process Flow Diagram(공정흐름도)
생산공정을 순서에 맞게 흐름도를 작성한 자료입니다. 공정 번호 및 순서가 P-FMEA 및 Control plan과 동일해야 합니다. FMEA에서 공정흐름에 변경이 있다면 해당 사항이 반영되어야 합니다. 기존 제품과 공정이 동일하며 원재료만 바뀌는 경우에는 기존 자료를 활용하여 준비해도 무방합니다.
6. Process FMEA(공정 FMEA)
위 말씀드린 공정흐름도, Control plan과 연계가 되어야 하며, D-FMEA와도 연계성이 확인되어야 합니다. 심사 시에 D-FMEA에서 특별 특성이 있을 경우 그와 관련된 공정도 특별공정으로 선정되도록 조치 이력이나 심화된 관리가 필요합니다.
7. Control Plan(관리계획서)
Control plan은 심사 시 가장 기본이 되는 사항으로 공정심사 진행 시 Control plan을 바탕으로 공정의 시작부터 끝까지 심사하게 됩니다. 공정의 관리 방법 및 관리 규격이 설정되어있어야 하며, Control plan 내에는 공정에서 관리하는 모든 요소가 포함되어야 합니다. 또한 공정관리의 항목 중 특별 특성 공정이 있다면 그에 대한 관리 요소는 SPC 관리 또는 전수검사가 진행되어야 합니다.
8. Measurement System Analysis(측정 시스템 분석)
생산 제품 또는 공정 관리 요소가 정확한 값으로 분석해내고 있는지 검증하는 방법입니다. 일반적으로 Gage R&R을 진행하여 편의, 안정성, 선형성을 확인하게 됩니다. 각 분석항목별로 Gage R&R 기준을 만족하는지 확인해야 하며, 기준을 만족하지 못하는 경우 개선 계획이 명확히 나와있어야 합니다.
9. Diamentional Result(치수 측정 결과)
설계 기록, Control plan에서 요구한 대로 측정 결과가 나오는지 확인한 결과를 말합니다. 일반적으로 최종 제품을 기준으로 자료를 제출하지만 공정품을 함께 요청하는 경우도 있습니다.
10. Material, Performance, Test Result(원료, 성능, 시험 결과)
원재료의 시험 성적서, 각종 성능 및 내구(고온, 저온, 고습, 저습 등의 가혹 환경) 시험의 결과를 포함합니다. 신뢰성 시험 결과로 보기도 하는 항목입니다. 외부 기관에서 진행한 시험 성적서가 있다면 그 항목으로 준비하시면 됩니다.
11. Initial Process Studies(초기 공정능력 조사)
양산에 준한 가동을 진행하여 생산된 제품에 대해 공정능력을 조사해야 합니다. 최소 100개 이상의 샘플로 25개 이상의 sub 그룹으로 나누어 Xbar-R 관리도를 작성하는 등의 공정능력을 산출하고 고객 공정능력 요구사항을 만족하면 됩니다. 만약 만족하지 못하는 경우, 고객으로부터 완전 승인은 받기 어려우며 잠정승인을 받은 뒤 개선을 통해 공정능력을 개선한 뒤에 완전 승인을 받을 수 있습니다. PPAP심사에서 가장 핵심이 되는 부분이니 철저히 준비하셔야 합니다.
12. Qualified Laboratory Documentation(자격 부여된 실험실 문서)
- 계측기 list, 분석 절차서 등의 자료로 준비하면 됩니다. 고객 규격을 위해 분석해야 하는 장비를 모두 포함하여야 하며 그에 따른 분석절차가 표준화되어있어야 합니다. 또한, 분석 절차뿐만 아니라 분석 환경, 분석 인원에 대해서도 관리하는 것을 증명해야 합니다. 현장 심사 시에 확인될 수 있는 부분이라면 분석 장비 목록으로 대체 가능하기도 합니다.
13. Appearance Approval Report(외관 승인 보고서)
외관 검사가 필요한 제품에만 한정됩니다. 외관, 색상 등의 검사가 필요한 제품만 준비하시면 됩니다.
14. Sample Product(양산 샘플)
샘플은 2개를 랜덤으로 택하게 됩니다. 고객이 허용할 경우 1개만 제출하여도 무방합니다.
15. Master Sample(마스터 샘플)
마스터 샘플은 고객이 한도 견본으로 사용할 수 있으며, 고객의 승인 일자가 표기되어야 합니다. 보존 연한에 대해서도 문서화된 기준을 따라야 합니다.
16. Checking Aids(검사 보조구)
검사에 사용되는 도구에 대한 List를 말합니다. 원료 검사 및 공정 검사 등에 사용되는 도구들을 말합니다. 12번 항목과는 차이가 있으니 혼선이 없으시길 바랍니다.
17. Customer Specific Requirement(고객 지정 요구사항)
-Certificate(인증서)(ISO or IATF16949 etc.)
-Packing Standard(포장 설명서)
-IMDS(International Material Data System)
-Safe Launch Control(초기 유동관리)
-Conflict Mineral Report(분쟁광물 미사용 확약서)
-Certificate of Analysis(COA)
-Bulk Material Checklist(벌크자재 체크리스트)
위 항목들이 별도 제출 사항에 해당하며 고객 요구사항에 따라 별도로 추가되는 사항이 있을 수 있습니다.
18. PSW(Part Submission Warranty)(부품 제출 보증서)
제출된 부품의 보증서로 제품 품번 및 Lot, 생산성 등의 정보를 입력합니다. 무게도 입력하는 칸이 있는데 10개의 샘플의 무게 평균을 입력하시면 됩니다. 최소 4자리를 입력해야 하니 참고하시길 바랍니다. PSW 내 작성해야 하는 항목은 모두 입력하셔야 합니다. PSW가 PPAP 산출물의 대표가 되는 문서입니다.
이 외에 추가되는 문서는 고객 지정 요구사항으로 고객 요구사항에 따라 준비하시면 됩니다. 위 산출물의 경우에도 변경 수준에 따라서 제출하지 않고 보관만 해도 되는 자료들이 있으니 PPAP 진행 전 반드시 변경 수준을 확인하시길 바랍니다. 제출하지 않더라고 내부적으로는 기록해야 하는 사항이니 준비는 하셔야 합니다.
'품질관리' 카테고리의 다른 글
MSA(측정시스템분석)의 기준과 평가(판정) 방법 (0) | 2022.11.29 |
---|---|
품질 비용 관리 항목 및 관리 방법(Quality related costs) (0) | 2022.07.15 |
[SPC 관리도] 슈하트 이상 판정 기준(규칙) - Shewhart (0) | 2022.07.08 |
[관리도] SPC 관리도의 종류와 선택 방법 - 어떤 관리도를 선택해야 할까? (0) | 2022.07.04 |
[계수형 관리도] 종류, 목적과 구분 방법 - np, p, U, C 관리도 (0) | 2022.07.01 |